Circuit Breakers
Circuit breakers are protective devices, which perform two primary functions:
- Open and close electrical circuits
- Current overload and short circuit protection of electrical equipment.
Similar to switch, circuit breakers are the primary way to energize and de-energize the circuit. Specialized circuit breakers can also be opened or closed remotely.
Overloading of electrical equipment, such as cables, can deteriorate insulation due to thermal stress cause by heat.
As current increases past the cables design rating, insulation will begin to deteriorate. Over an extended period of time, leakage current will increase, eventually causing it to fail.
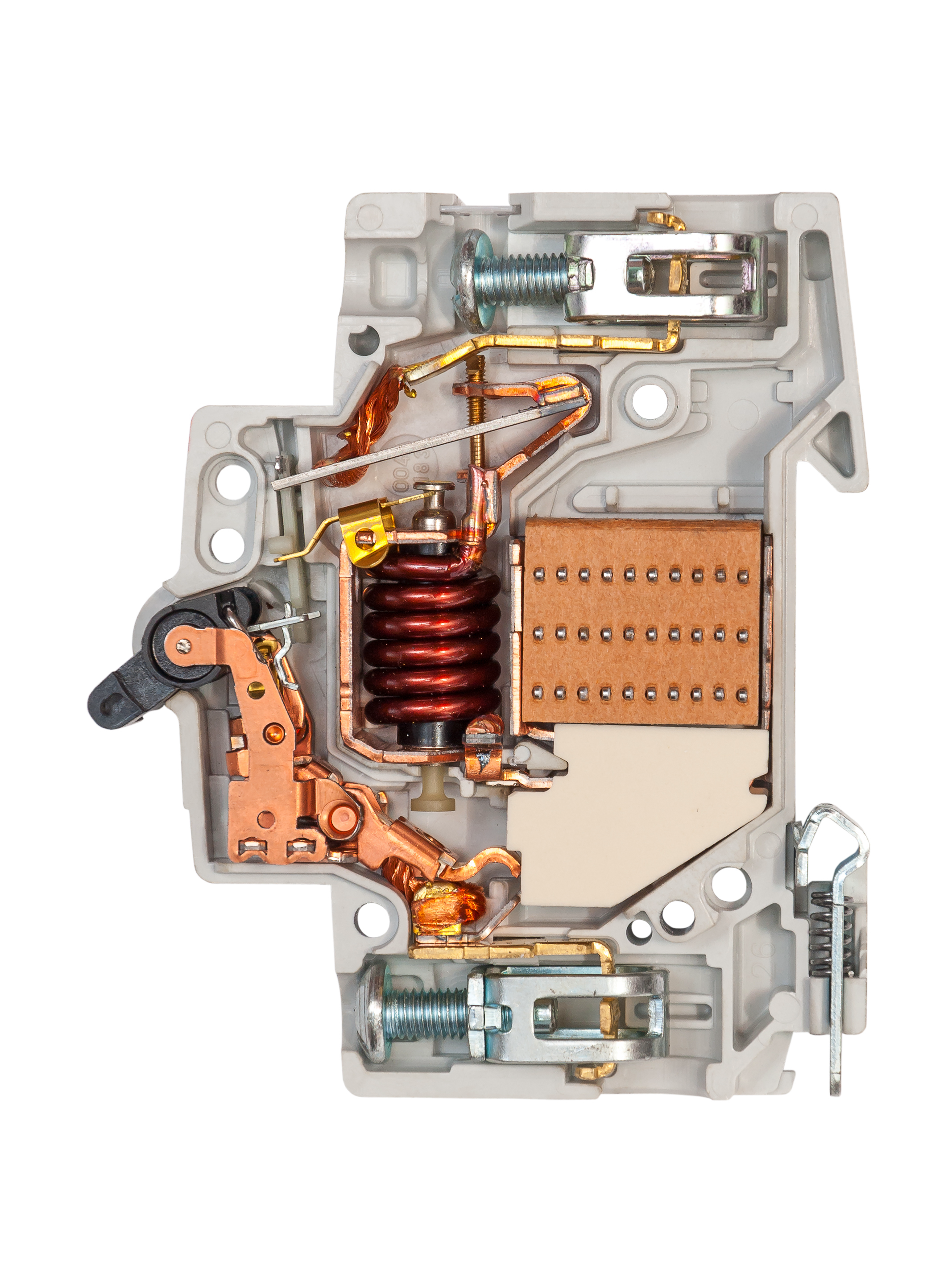
Circuit Breakers Types | |
---|---|
Low Voltage, less than 600V | |
Molded-Case Circuit Breakers (MCCBs) |
MCCB are the most widely used type of circuit breakers. They are available in a wide range of ratings and are generally used for low-current, low-energy power circuits. They can be found in residential, commercial, and industrial facilities. MCCB are simple mechanical devices which employ a thermal bimetallic element that has inverse time–current characteristics for overcurrent protection and a mechanical magnetic trip element for short-circuit protection
Continue reading
Demulsifi cation occurs when the tiny droplets unite to form larger drops, which sink to the bottom and form a pool of free water. Water in the free state may be readily removed by fi ltering or centrifugal treatment. However, dissolved water is not removed by centrifugal treatment |
Insulated-Case Breakers |
Insulated-case circuit breakers are a type of molded-case breaker constructed with glass reinforced insulating material for increased dielectric strength. These breakers can have Electromechanical trip units which was discussed above, or an Electronic trip units offer capabilities such as programming monitoring diagnostics communications system coordination and testing that are not available on thermal magnetic trip units. |
Motor Circuit Protector (MCP) |
Magnetic-trip-only breakers have no thermal element. Such breakers are principally only used for isolating the circuit and short-circuit protection. Molded-case breakers with magnetic only trips find their application in motor circuit protection. MCP's can be found inside Motor Control Center (MCC). They are typically placed inside a cubical or enclosure, along with motor control elements and a motor overcurrent device; commonly knows as a heater. |
Fixed or Draw-Out Power Circuit Breakers |
Heavy-duty power circuit breakers employ spring-operated, stored-energy mechanisms for quick-make, quick-break manual or electric operation. Generally, these breakers have draw-out features whereby individual breakers can be put into test and fully de-energized position for testing and maintenance purposes. ![]() |
Electronic Trip | ||||||||||||||||||||||||||||
---|---|---|---|---|---|---|---|---|---|---|---|---|---|---|---|---|---|---|---|---|---|---|---|---|---|---|---|---|
![]() ![]() |
||||||||||||||||||||||||||||
|
||||||||||||||||||||||||||||
Circuit Breaker Manufacturers:
Voltage, Current, Frequency
15, 20, 25, 30, 35, 40, 45, 50, 60, 70, 80, 90, Additional standard fuse sizes are 1, 3, 6, 10, and 601 amps. Industrial-grade MCCBs are available in frame sizes from 100 amperes to 3000 amperes. ICCBs are available in frame sizes from 400 to 5000 amperes. The 400-ampere-frame ICCB is typically the same size and cost as the 800-ampere frame but is equipped with smaller-ratio current sensors. PCBs are available in frame sizes from 800 to 5000 amperes. Frame Ratings:Ampere Frame [AF] it is the rating breaker current [maximum. current which the breaker will withstand for a long. time]. Ampere Ratings:Ampere trip [AT] it is the current set to trip the. circuit [usually from 60% up to 100% of the AF]
![]() ![]() ![]()
The short circuit rating of a circuit breaker is defined by its interrupting capacity 10K, 25K, 35K, 42K, 65K, 100K, 200KAIC
Overloading of electrical equipment, such as cables, can deteriorate insulation due to thermal stress cause by heat. Auxilary Devices
For electrical operation, MCCBs typically use a motor or solenoid operator to drive the handle mechanism. Motor operators have closing and opening times of several cycles to several seconds. Solenoid operators have operating times that vary from six cycles to several cycles. ICCBs and PCBs have internal motor operators that charge the closing springs within a few seconds. This charging time is independent of the circuit breaker closing and tripping time. The closing and tripping solenoid coils can close or open the circuit breaker in five or fewer cycles. Five-cycle closing is necessary. ![]() Under VoltageThe undervoltage release instantaneously opens the circuit breaker when its supply voltage drops to a value between 35% and 70% of its rated voltage. If there is no supply to the release, it is impossible to close the circuit breaker, either manually or electrically. Any attempt to close the circuit breaker has no effect on the main contacts. Circuit breaker closing is enabled again when the supply voltage of the release returns to 85% of its rated value.
Series RatingSeries ratings permit the application of two or more circuit breakers in series, in accordance with the National Electrical Code (NEC) [16], at locations in a power system where the downstream circuit breaker interrupting capacity for an application that is not series-rated is lower than the available fault current. This is possible because both breakers share the high current fault interruption. Series-rated circuit breakers are UL tested as a combination of a fully rated upstream device, either a circuit breaker or a fuse, and a lower-rated downstream device. The upstream device in a series-rated system is always fully rated, with an interrupting capacity equal to the available fault current, while the downstream device may have a lower interrupting capacity. This allows a system design less costly than systems that use devices fully rated for the available fault current. Zone InterlockZone-Selective Interlocking (ZSI), or zone restraint, has been available since the early 1990s. ZSI is designed to limit thermal stress caused by shortcircuits on a distribution system. ZSI will enhance the coordination of the upstream and downstream molded case circuit breakers for all values of available short-circuit current up to the instantaneous override of the upstream circuit breaker Circuit breakers equipped with zone interlocking on short delay with no restraining signal from a downstream device will have the minimum time band applied regardless of setting, this is sometimes referred to as the maximum unrestrained delay. When the instantaneous function is disabled, a short-time delay override is used to instantaneously trip circuit breakers in the event of a significant short circuit. This is called the short-time withstand rating and is represented on the trip curve as an absolute ampere value. Kirk InterlockA Kirk interlock is a keyed interlock. Each Kirk key has a serial number on it that must be matched to the tumbler. Only one key with the serial number should be in the substation. Kirk interlocks also are used to ensure proper sequences are followed in switching routines. Kirk interlocks can be used as a mechanical or electrical interlock. When used for electrical interlocking, the Kirk interlock operates an auxiliary switch. For example, a Kirk interlock could be used to ensure a transformer low side breaker is opened prior to opening a low side transformer disconnect switch. In this case, the Kirk key could only be removed from the low side transformer circuit breaker while it is in the open position. Then the Kirk key would be removed and placed in the matching serial number tumbler for the disconnect switch and turned, allowing the disconnect switch to be operated. |
Circuit Breaker Tests | |
---|---|
|
|
Test Equipment
Visual Mechanical Inspection:
Continuous Amps (Ir) varies . Ir is a percentage of the circuit breaker’s nominal rating (In). Continuous amps can be adjusted from of the circuit breaker’s nominal rating. The purpose of this test is to determine that the trip device will open the circuit breaker to which it is applied. This test can usually be performed by injecting 150%–300% current of the coil rating into the trip coil. The test equipment used should be able to produce the required current and be reasonably sinusoidal. Circuit breaker short-time-delay (STD) mechanisms allow an intentional delay to be installed on low voltage power circuit breakers. Short-time-delays allow the fault current to flow for several cycles, which subjects the electrical equipment to unnecessarily high mechanical and thermal stress The magnetic (INST) trip should be checked by selecting suitable current to ensure that the breaker magnetic feature is working. The diffi culty in conducting this test is the availability of obtaining the required high value of test current. Ground Fault Protection:Zero SequenceCircuit feeders are fed through a current transformer. A zero sequence relay or circuit breaker trip unit ensures that the circuit current feeding the load will return to the source returns on those same conductors . If the current is returning to the source through a different path (usually ground), the ground-fault relay will detect this difference. If the diffrence in current exceeds a pre-determined amount for a pre-determined amount of time, the ground-fault relay will operate.
\[I_{a}+I_{b}+I_{c}-I_{n}=0\]
Summation MethodDirect measurement of all phase and neutral current through a protection device's current transformers is evaluated. All phase currents feeding a load should return to the source. A ground fault some where downstream will create a difference in the returning current.
\[I_{a}+I_{b}+I_{c}=I_{n}\]
Primary Current TestStationary and moving contacts are built from alloys that are formulated to endure the stresses of electrical arcing. However, if contacts are not maintained on a regular basis, their electrical resistance due to repeated arcing builds up, resulting in a signifi cant decrease in the contact’s ability to carry current. Excessive corrosion of contacts is detrimental to the breaker performance. One way to check contacts is to apply DC and measure the contact resistance or voltage drop across the closed contacts. The breaker contact resistance should be measured from bushing terminal to bushing terminal with the breaker in closed position. Secondary Injectoon TestingSolid-state trip units can be tested via secondary current injection using a test set specifically designed for the device to be tested. The main shortcoming of the secondary current injection test method is that only the solid-state trip unit logic and components are tested. Unlike primary injection, this test method does not verify the current sensors, wiring, or circuit breaker current carrying components. This is the main reason why the primary injection test method has superiority over secondary injection testing. The protective functions of the electronic trip device can be tested, but the trip device won't send a trip signal to the circuit breakers trip actuator. This test can be performed while the circuit breaker is energized and carrying load current because a no-trip test won't cause the circuit breaker to open. The protective functions of the electronic circuit are tested just like a no-trip mode test, except the trip unit will send a signal to the circuit breakers trip actuator. This will cause the circuit breaker to open, which is why this test is typically performed only when a circuit breaker is withdrawn from its compartment and therefore disconnected from the switchgear bus. Contact ResistanceStationary and moving contacts are built from alloys that are formulated to endure the stresses of electrical arcing. However, if contacts are not maintained on a regular basis, their electrical resistance due to repeated arcing builds up, resulting in a signifi cant decrease in the contact’s ability to carry current. Excessive corrosion of contacts is detrimental to the breaker performance. One way to check contacts is to apply DC and measure the contact resistance or voltage drop across the closed contacts. The breaker contact resistance should be measured from bushing terminal to bushing terminal with the breaker in closed position. This is the primary circuit resistance test that was discussed in Section 8.7.2 for low-voltage power circuit breakers. This test consists of applying a DC across the closed circuit breaker contacts and measuring the voltage drop due to the contact resistance. Excessive voltage drop indicates abnormal conditions such as contact and/or connection erosion and contamination. This test is similar to the circuit breaker contact resistance measurement test described in Section 7.4.5 for medium-voltage breakers. The manufacturers of MCCBs should be consulted in order to fi nd the acceptable millivolt drop values for particular breakers being tested. It is recommended that large breakers be tested with DC of at least 100 A and smaller breakers be tested at rated (or below rated) currents. The measured values should be compared among three phases of the breaker under test, or with values of breakers of similar size or with manufacturer’s recommended values to assess whether the contacts need to be replaced or dressed. Where:
Insulation Resistance:DESCRIPTION:This test is performed at or above rated voltage to determine if there are low resistance paths to ground or between winding to winding as a result of winding insulation deterioration. PURPOSE:This test is made to verify the condition of the insulation of the circuit breaker. A minimum of 1000 V test voltage should be used for low-voltage (600 V class) breakers for making this test. It would be preferable to use a DC test voltage that is at least 1.5–1.6 times the peak AC voltage of the circuit breaker. Tests should be made between pole to ground, between adjacent poles with circuit breaker contacts closed, and between phase-to-load terminal with breaker in open position. A minimum value of 1 MΩ is considered safe to prevent a fl ashover. Resistance values below 1 MΩ should be investigated for possible trouble.
EATON +310ND, CND, HND, CHND, CNDC Equipped with Type NES Digitrip RMS 310 Trip units with I2T Ramp Short Time Delay (Phase Protection) |
NETA Test Procedure | |
---|---|
NETA ATS7.6.1.1 Circuit Breakers, Air, Insulated-Case/Molded-CaseA. Visual and Mechanical Inspection:
B. Electrical Tests:
C. Test Values – Visual and Mechanical
D. Test Values – Electrical
NETA ATS7.6.1.2 Circuit Breakers, Low-Voltage PowerA. Visual and Mechanical Inspection:
B. Electrical Tests:
C. Test Values – Visual and Mechanical
D. Test Values – Electrical
NETA MTS7.6.1.1 Circuit Breakers, Air, Insulated-Case/Molded-CaseA. Visual and Mechanical Inspection:
B. Electrical Tests:
C. Test Values – Visual and Mechanical
D. Test Values – Electrical
NETA ATS7.6.1.2 Circuit Breakers, Low-Voltage PowerA. Visual and Mechanical Inspection:
B. Electrical Tests:
C. Test Values – Visual and Mechanical
D. Test Values – Electrical
NETA ATS / MTS
TABLE 100.1
![]() NETA ATS / MTS
TABLE 100.7
![]() NETA ATS / MTS
TABLE 100.8
![]() NETA ATS / MTS
TABLE 100.12
![]() ![]() NETA ATS / MTS
TABLE 100.20
![]() ![]() |